The use of 4th axis Vertical Machining Centers (VMC) has significantly advanced precision manufacturing, allowing for the creation of intricate components with improved accuracy and efficiency.
For industries that rely on high-precision parts, like aerospace, automotive, and medical, 4-axis VMC job work has become an invaluable asset. However, while 4th axis VMC machining brings several advantages, it also presents unique challenges. Understanding and addressing these challenges is key to maximizing the benefits of 4-axis VMC technology.
Table of Contents
What is 4th Axis VMC Machining?
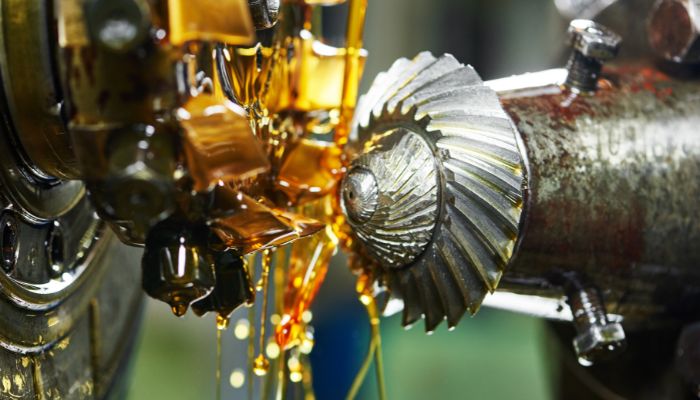
To fully understand the challenges in 4th axis VMC machining, let’s first discuss how this technology works. A standard VMC operates on three axes: X (left-right), Y (forward-backward), and Z (up-down).
In 4-axis VMCs, an additional axis, known as the A-axis, is introduced, which allows the workpiece to rotate around the X-axis. This extra rotation enables the machine to work on multiple sides of a component in one setup, making it ideal for creating complex geometries.
For example, in a 4-axis VMC job work setup, components with curves, holes at precise angles, or features on multiple sides can be easily manufactured without the need for multiple setups.
Despite its versatility, 4-axis VMC machining requires careful handling to achieve accurate results and can be challenging even for experienced operators.
Common Challenges in 4th Axis VMC Machining:
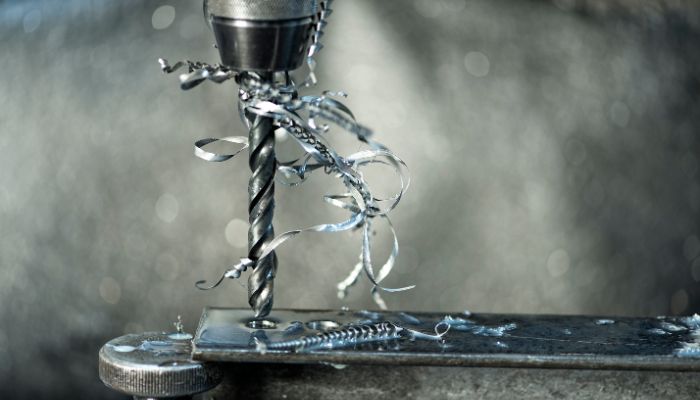
1. Complex Programming and Setup
The 4th axis adds a layer of complexity to the programming and setup of the VMC. Unlike standard 3-axis machining, where movements are limited to three directions, the additional A-axis introduces rotational movements that need precise calibration. This extra complexity can make programming more time-consuming and increase the chances of errors.
Solution: Experienced programmers and advanced software can help address this issue. Many VMC components manufacturers, like Global Precision Pvt Ltd, use specialized software and simulation tools to test and verify programs before running them on actual workpieces. This helps reduce errors and improves efficiency.
2. Tool Wear and Breakage
The increased complexity of 4th axis VMC machining components can lead to higher tool wear. As tools are subjected to more varied cutting angles and speeds, they experience greater stress, which can lead to faster wear or even breakage if not carefully monitored.
Solution: To address this, it’s essential to use high-quality tools designed for multi-axis machining. Regular tool inspection and maintenance are also critical. Many manufacturers, including Global Precision Pvt Ltd, use tool-monitoring systems that detect wear early and signal when tools need replacement. This helps maintain consistent quality and extends tool life.
3. Alignment and Calibration
Proper alignment and calibration are crucial for 4th axis VMC machining to achieve the required precision. The extra axis requires accurate positioning of the workpiece; even slight misalignments can lead to errors in the finished product. Calibration is especially critical when switching between different components or setups.
Solution: Frequent calibration and verification checks can help maintain accuracy. Precision manufacturers like Global Precision Pvt Ltd utilize advanced measuring equipment and automated calibration tools to ensure alignment before each job. This not only ensures accuracy but also saves time by reducing manual adjustments.
4. Increased Setup Time
With an additional axis to control, setting up 4-axis VMC jobs can take longer than traditional 3-axis jobs. This setup time includes calibrating the rotation of the A-axis, securing the workpiece in the correct orientation, and making sure all tools are accurately aligned.
Solution: Efficient fixtures and work-holding solutions can reduce setup time. At Global Precision Pvt Ltd, the use of customized fixtures allows for quick, secure workpiece positioning, helping to minimize setup time and keep production moving efficiently.
5. Difficulty in Reaching Tight Tolerances
While 4-axis VMCs offer greater flexibility in shaping complex geometries, achieving tight tolerances can still be challenging, especially when dealing with intricate designs. Any movement or vibration in the extra axis can impact the accuracy of cuts, making it harder to achieve the desired tolerances.
Solution: One effective approach is using rigid work-holding solutions and stable machining conditions. Global Precision Pvt Ltd prioritizes vibration-dampening fixtures and carefully monitors the machining environment to maintain consistent tolerances. Advanced simulation software also helps in predicting how the tool and machine will behave, allowing for pre-emptive adjustments.
6. Workpiece Stability and Fixturing
The extra rotation in 4-axis machining can make it difficult to keep the workpiece stable. If the workpiece shifts during rotation, it can lead to errors or damaged parts. Fixturing in 4-axis VMC job work thus becomes more complicated and needs to be handled with great care.
Solution: Custom fixtures are designed for specific parts to ensure stability. Many VMC components manufacturers, like Global Precision Pvt Ltd, invest in specialized fixturing solutions to securely hold the workpiece during the entire machining process. These fixtures provide the stability needed for intricate jobs, allowing for better accuracy and reducing the risk of shifting.
7. Tool Access and Reach
While the 4th axis allows greater flexibility, it can also limit tool reach in certain angles. For components with deep cavities or tight corners, ensuring that the tool can reach all areas without interference is a significant challenge.
Solution: Global Precision Pvt Ltd tackles this challenge by selecting the right tools for each specific job. Long-reach tools and angled tooling solutions can help overcome reach limitations, while careful planning ensures that tools are accessible to all parts of the component without risk of interference.
How Global Precision Pvt Ltd Tackles 4th Axis VMC Challenges:
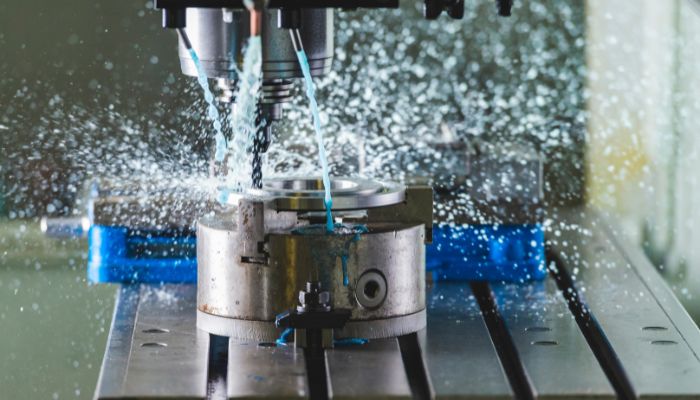
As a leading VMC components manufacturer, Global Precision Pvt Ltd has developed expertise in overcoming the challenges of 4-axis VMC machining. Here are some strategies they use to consistently deliver high-quality 4th axis VMC machining components–
1. Advanced Software and Skilled Programming
Utilizing the latest CAD/CAM software, Global Precision Pvt Ltd ensures precise programming and reduces the risk of errors in complex 4-axis jobs.
2. Tool Management Systems
They employ advanced tool-monitoring systems to detect and address tool wear early. This prevents costly breakages and keeps the manufacturing process smooth and efficient.
3. Custom Fixturing and Calibration
By designing custom fixtures and performing regular calibration checks, they ensure workpiece stability and alignment, which are critical for achieving accuracy in 4-axis machining.
4. Strict Quality Control
Each component produced undergoes a thorough inspection to ensure it meets the tight tolerances required. With a commitment to quality, Global Precision Pvt Ltd has established a reputation as a reliable 4-axis VMC job work provider.
Conclusion
4th axis VMC machining opens up a world of possibilities in precision manufacturing, allowing for the production of complex components with increased accuracy. However, it comes with its own set of challenges, from programming complexities to maintaining tight tolerances and tool wear.
Overcoming these challenges requires a combination of advanced technology, skilled operators, and effective quality control measures.For industries seeking high-quality 4-axis VMC machining components, Global Precision Pvt Ltd stands out as a trusted partner.
With their experience, expertise, and commitment to quality, they continue to deliver exceptional results, helping businesses leverage the full potential of 4-axis VMC technology.