The manufacturing world is changing rapidly, driven by constant innovations in CNC technology, rotor shaft design, and forging techniques. The latest CNC trends are helping manufacturers produce more precise, durable, and cost-effective components.
We will highlight the role of reputable companies such as Global Precision Pvt Ltd, and discuss the offerings from leading CNC machined components manufacturers. Let’s find out the latest trends in CNC machining, discuss the recent improvements in rotor shafts, and look into the world of forging technologies.
Table of Contents
The Rising Trend of CNC Technology
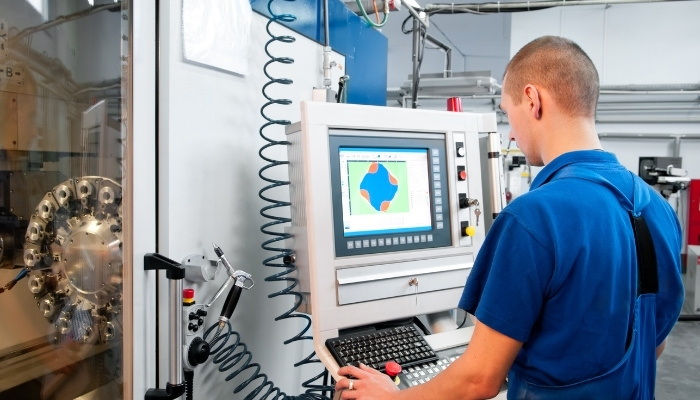
In modern manufacturing, CNC (Computer Numerical Control) machining has been at the forefront for decades. Today, CNC technology is evolving faster than ever before, integrating new tools and techniques that lead to higher precision, speed, and efficiency.
1. Increased Automation and Smart Manufacturing
One of the major trends in CNC machining is increased automation. Advanced CNC machines are now more automated than ever, with smart systems that can self-diagnose and even perform minor repairs. This means manufacturers can achieve higher productivity and maintain excellent quality control. Many CNC machined components manufacturers are adopting these smart systems to minimize downtime and ensure consistent production quality.
2. Integration with Industry 4.0
Another significant trend is the integration of CNC machines with Industry 4.0 technologies. With the help of IoT (Internet of Things) sensors, big data analytics, and cloud computing, manufacturers are now able to monitor machine performance in real-time. This integration allows for predictive maintenance and better planning of production cycles, leading to increased efficiency. Many CNC components manufacturer companies are supporting these technologies to stay competitive and fulfill the ever-growing demand for precision components.
3. Customization and Flexibility
Customization has become a vital factor in the modern manufacturing process. CNC machining now offers more flexibility to produce custom parts quickly. With the latest software advancements, engineers can efficiently change strategies to fulfill distinct client necessities. This trend is particularly important for sectors such as aerospace, automotive, and medical devices, where precision is paramount. Whether it’s through CNC Turned Components or CNC Milling Components, manufacturers are finding new ways to cater to bespoke production demands.
Advancements in Rotor Shafts
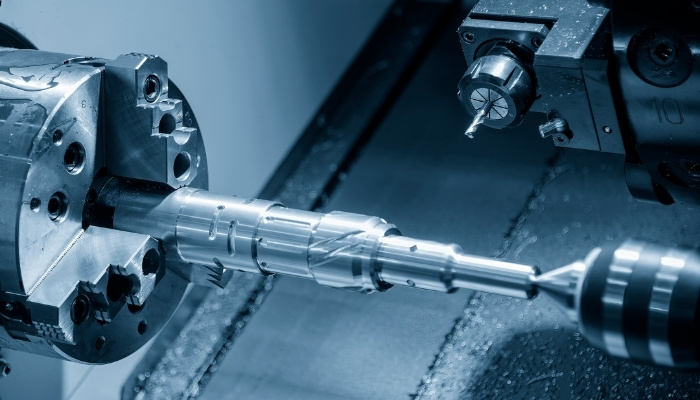
Rotor shafts are critical components in various machines, including turbines, engines, and industrial equipment. Recent innovations in design and material science are making rotor shafts more reliable and efficient than ever.
1. Enhanced Materials and Durability
One of the major advancements in rotor shaft technology is the usage of developed materials. New alloys and composite materials have significantly improved the durability and implementation of rotor shafts. These materials provide better resistance to wear, corrosion, and high temperatures. By utilizing these advanced materials, manufacturers are able to produce rotor shafts that not only last longer but also function more useful under extreme circumstances.
2. Precision Manufacturing Techniques
Modern rotor shafts require high levels of precision, which is where the latest CNC machining technologies come into play. High-precision CNC turning and milling techniques ensure that rotor shafts meet strict quality standards. Companies that specialize in CNC Turned Components and CNC Milling Components have developed processes that can achieve incredibly tight tolerances. This precision is essential for rotor shafts, as even small imperfections can lead to significant performance issues.
3. Improved Design and Efficiency
Current improvements in computer-aided design (CAD) and simulation software have revolutionized the way rotor shafts are designed. Engineers can now affect the pressures and stresses on a rotor shaft before it is manufactured. This allows for the optimization of the design, resulting in elements that are lighter, more powerful, and more efficient. The improved designs help in reducing energy losses in machines and contribute to overall operational efficiency.
4. Impact on Various Industries
The improvements in rotor shaft technology are having a wide-ranging effect on numerous industries. In the energy sector, for example, more efficient rotor shafts lead to better performance of wind turbines and hydroelectric generators. In the automotive and aerospace sectors, enhanced rotor shafts contribute to improved engine performance and reduced maintenance costs. The ripple effect of these improvements is a significant boost in overall productivity and reliability.
Forging Technologies – A Timeless Process Reinvented
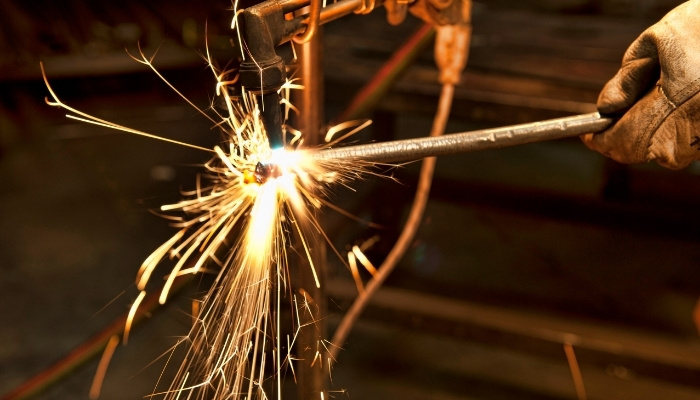
Forging has been used for centuries to build robust and durable metal parts. Today, modern forging techniques are being combined with advanced CNC machining to produce high-quality components for a variety of applications.
1. Modern Forging Techniques
Modern forging techniques have evolved significantly, thanks to the integration of CNC technology. CNC-controlled forging presses now offer greater precision and repeatability than ever before. This means that the final products have a consistent quality, which is crucial for high-performance applications. The collaboration between traditional forging methods and modern CNC machining has led to the production of components that are both robust and highly precise.
Benefits of Combining CNC and Forging
Combining CNC machining with forging technologies offers several advantages –
- Enhanced Strength and Durability – Forging processes create a dense, uniform grain structure in the metal, which improves the strength and durability of the part.
- Precision and Accuracy – CNC machining ensures that the forged parts meet precise dimensions and tolerances, which is vital for complex assemblies.
- Cost-Effectiveness – While the initial investment in CNC-controlled forging might be high, the long-term benefits of reduced waste, increased efficiency, and fewer defects make it a cost-effective solution.
2. Applications Across Industries
Forged components are used in a wide range of industries, including automotive, aerospace, construction, and heavy machinery. In these sectors, the components often face severe conditions such as high force, temperature, and mechanical stress. The combination of CNC precision and traditional forging strength ensures that these parts perform reliably under such demanding conditions.
Role of Global Precision Pvt Ltd
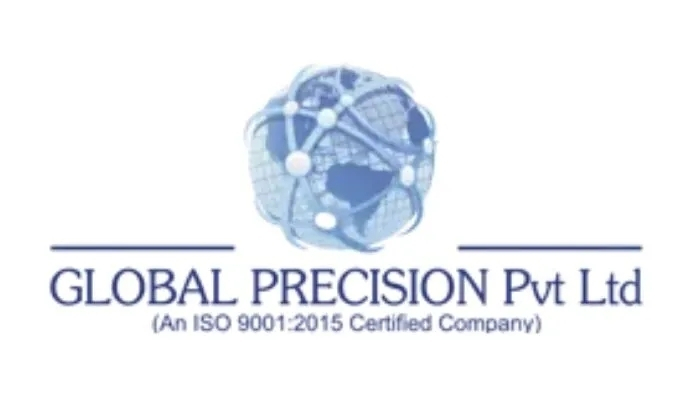
Companies like Global Precision Pvt Ltd are at the forefront of integrating CNC machining with advanced forging technologies. They work closely with industries to produce components that fulfill the highest criteria of quality and precision. As a leading name in the industry, Global Precision Pvt Ltd provides services that span from the production of CNC Turned Components to CNC Milling Components, ensuring that every piece produced meets strict industry standards.
The Future of Manufacturing
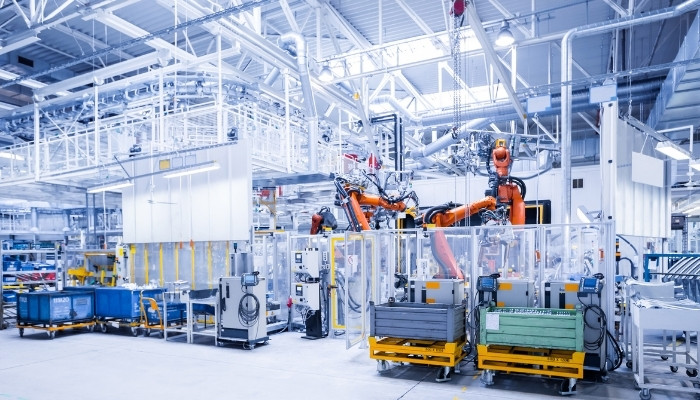
The future of manufacturing is encouraging, with ongoing improvements in CNC technology, rotor shaft design, and forging processes. Manufacturers are adopting new technologies that improve productivity, reduce waste, and improve overall product quality.
1. Emphasis on Sustainability
One of the key trends for the future is sustainability. The manufacturing enterprise is increasingly concentrated on decreasing its environmental footprint. Advanced CNC machining and forging processes are being optimized to decrease energy consumption and underestimate material waste. By adopting these eco-friendly practices, companies not only protect the environment but also improve their operational efficiency.
2. Continued Integration of Digital Technologies
The integration of digital technologies in manufacturing will continue to grow. With the increasing use of AI, machine learning, and advanced data analytics, CNC machines and forging equipment will become even more efficient. These digital tools will enable manufacturers to anticipate maintenance requirements, optimize production programs, and improve overall quality control. This trend is expected to set new benchmarks in the industry.
3. Collaboration Between Traditional and Modern Techniques
The successful manufacturing strategies of tomorrow will likely apply a combination of standard approaches and contemporary innovations. Forging, a process that has been used for centuries, when combined with the precision of CNC machining, can produce components that are both strong and incredibly accurate. This collaboration is already being seen in the production practices of many leading companies, including Global Precision Pvt Ltd.
Conclusion
The manufacturing industry is experiencing a transformation forced by the latest CNC trends, advancements in rotor shafts, and modern forging technologies. With increased automation, integration of digital tools, and enhanced materials, the future of CNC machining looks promising. Manufacturers are now better furnished to fulfill the demands for precision, efficiency, and durability.
Leading CNC machined components manufacturers and CNC components manufacturer experts are at the heart of this revolution, offering advanced solutions like CNC Turned Components and CNC Milling Components that meet the highest industry standards. Companies like Global Precision Pvt Ltd are setting new benchmarks in quality and innovation, ensuring that every component they produce is reliable and meets the demands of modern industry.