Composite CNC machining is a cornerstone of the modern manufacturing industry, and its evolution has led to significant improvements for CNC machined components manufacturers. Pushing the boundaries of precision and efficiency, CNC machining has allowed them to produce products as they desire.
From constructing spacecraft to producing furniture, their impact on the manufacturing and precision engineering industries is significant. This blog post will feature a comprehensive overview of composite materials, their benefits in composite CNC machining, etc. that will help you explore the advanced composite CNC machining process.
Table of Contents
What are Composite Materials?
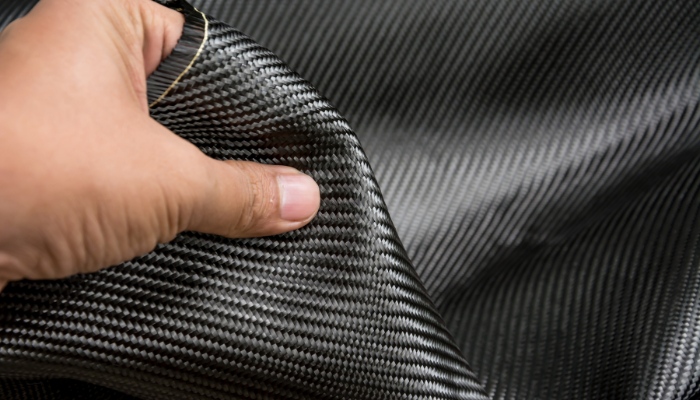
A synthetic material that is made after combining two or more materials with different unique properties is called composite material. A composite material is special as it exhibits properties of both materials, such as flexibility, strength, durability, resistance, etc. Their greater mechanical, physical, and chemical properties than standard engineering metallic materials make them a vitally important part of CNC machining.
What are The Three Primary Components of Composite Materials?
Three primary components of composite materials are the determining factors for their performance and applications for a CNC components manufacturer, which are:
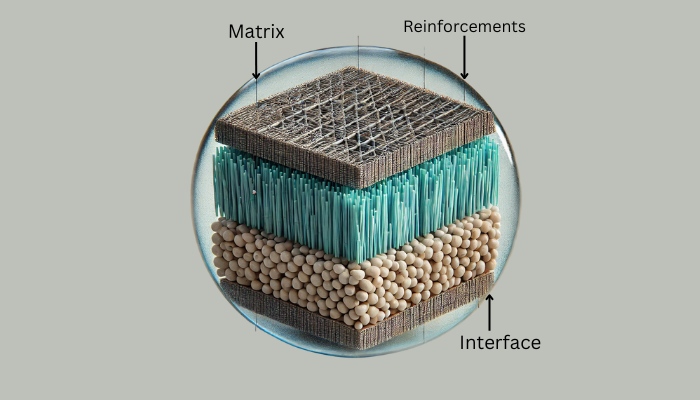
1. Matrix:
A matrix is a primary component of a composite material that can be defined as a continuous phase in a composite material that holds the reinforcement in place. Binding fibers together, distributing the load, and protecting them from environmental damage are the primary functions of a matrix. There are three main types of matrices:
- The polymer matrices are most popular as they have low cost and have good temperature and resistance properties. Additionally, they’re light in weight, so they are used in the production of consumer items and vehicle parts.
- Ceramic matrices with stability at high temperatures, superior compressive strength, and high melting points make them popular in the aerospace industry.
- Metal matrices with properties like superior temperature resistance, stiffness, high strength-to-weight ratio, high wear resistance, etc. make them popular in automotive, aerospace, and other industries.
2. Reinforcements:
Reinforcements are constituents of composite materials that improve their stiffness, strength, and other mechanical properties. Additionally, heat resistance and corrosion resistance are also provided by it. It can be described as the discontinuous or dispersed phase in a composite material that can be long or woven fibers or short particles. Three typical types of reinforcement fibers include glass, carbon, and aramid fibers. Among these, carbon fibers are considered the strongest and stiffest reinforcement fiber.
3. Interface:
The region in a composite material where the matrix and reinforcement meet is the interface. This interphase zone between the other two constituents of composite material greatly contributes to the performance of a composite material. Interface facilitates interaction between fiber and matrix through different mechanisms, including mechanical coupling, physical coupling, covalent bonding, etc. It influences the strength, modulus, toughness, and interaction of a composite material with its surroundings.
Types of Composite Materials Used in CNC Machining:

The following composite materials are typically utilized by CNC machined components manufacturers in the CNC machining industry, which are selected due to their cost-effectiveness and special properties.
1. Carbon Fiber Reinforced Polymer (CFRP)
This composite material is composed of carbon fibers and polymer matrix and has special properties like lightweight, durability, great strength-to-weight ratio, etc. From manufacturing automobile parts to sporting goods, like fishing rods or tennis rackets, they’re extensively used in composite CNC machining.
2. Glass Fiber Reinforced Polymer (GFRP)
This composite material has glass fibers embedded in the polymer resin matrix with great tensile strength, flexibility, chemical resistance, etc.
3. Aramid Fiber Reinforced Polymer (AFRP)
It is a synthetic organic composite material with desirable properties like strength, lightweight, low flammability, etc., and is composed of aramid fibers and polymer matrix. It is used in the manufacturing of aerospace components, military helmets or gloves, sporting goods, thermoplastic pipes, etc.
4. Basalt Fiber Reinforced Polymer (BFRF)
It is an eco-friendly composite material composed of polymer resins and basalt fibers, which are made from natural volcanic rock, basalt. It exhibits superior acid-alkali resistance, electrical, and other properties.
5. Metal Matrix Composites (MMC)
These are lightweight and structural composite materials made from metal matrix and reinforcing particles. From high-end sports equipment to aircraft and spacecraft components, they are greatly in the CNC machining industry by a CNC components manufacturer.
Natural fiber-reinforced polymer, hybrid composites, Boron fiber-reinforced polymer, etc. are some other common types of composite materials used in composite CNC machining.
Considerations for Selecting a Composite for CNC Machining:
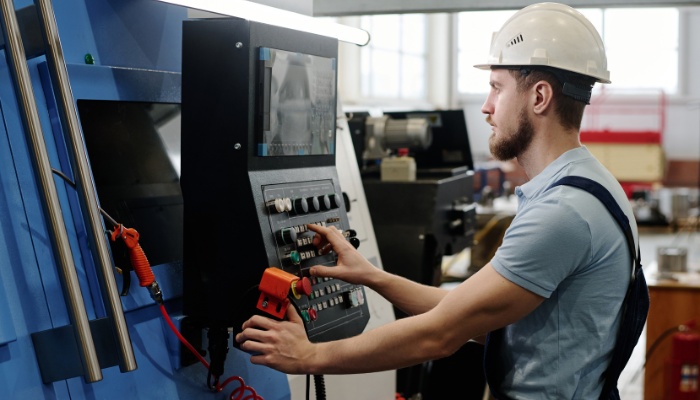
- You need to choose a composite material that will be suitable for the intended application of the part it will make. Additionally, consider the operating environment or conditions the part will be exposed to, such as moisture, chemicals, high temperatures, etc.
- Assess the chemical, mechanical, and physical properties of the materials, which is crucial for a particular CNC component production.
- Considering the machinability of the composite material is essential before selecting it. Ensure the material can be easily machined, as they help in saving maintenance costs, reducing machining downtime, and increasing production efficiency.
- Determine the cost-effectiveness of the material based on the scrap material it will produce. You can take expert guidance for making an informed decision and making a lucrative investment.
Advantages of Composite CNC Machining:
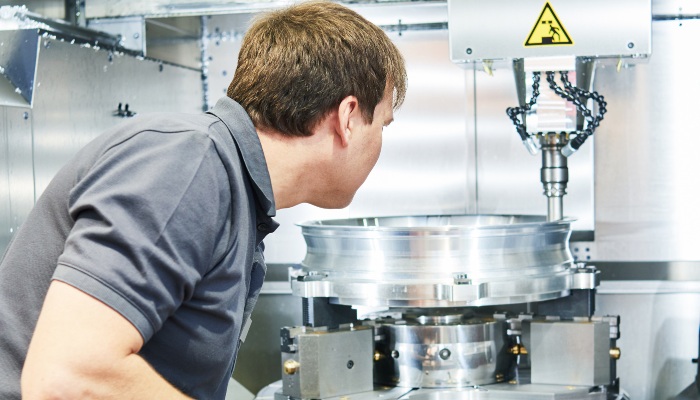
1. Precision
Composite CNC machining can be highly beneficial in the production of components with complex shapes with great precision and accuracy. This merit makes it an important part of the aerospace, medical, and defense industries, where even small variations can cause serious consequences.
2. Speed
Composite CNC machining greatly assists CNC machined components manufacturers in speeding up the production of parts. Even with projects involving intricate designs, they result in quick production of parts with short lead times.
3. Safety
The direct involvement of human labor with cutting, shaping, or other tools is decreased with composite CNC machining. It has significantly increased the safety of workers and reduced the possibility of mishaps.
4. Flexibility
Without any need for custom tooling or a special designing process, composite CNC machining can manufacture a wide variety of geometries or designs by switching different composite materials quickly.
5. Durability
Composite CNC machined components are more durable than components made with less precise technology.
6. Cost Savings
By reducing labor costs, errors in manufacturing, material waste production, etc., it assists in cost savings for a CNC components manufacturer. Additionally, mass production can be easily achieved by composite CNC machining as it delivers uniform outputs.
Conclusion:
The unique properties combination of composite materials makes them stronger and stiffer, which makes composite CNC machining popular in the manufacturing and precise engineering industry. By working together with Global Precision Pvt. Ltd., you can get access to efficient and innovative composite CNC machining technology at competitive rates.
We, being the leading high-precision machining and manufacturing company, have over 13 years of expertise and a track record of offering the best services to CNC machined components manufacturers globally. From the production of extensive designs with ease and accuracy to superior quality and efficient components, composite CNC machining technology can positively impact your business.