The world of manufacturing is constantly evolving due to new technology and rising demands for accuracy and productivity. At the forefront of this revolution is CNC machining, which has transformed sectors like automotive and aerospace.
As a leading provider of CNC machined components manufacturers and CNC components manufacturer, Global Precision Pvt Ltd is committed to staying at the forefront of this technological advancement.
In this blog post, we delve into the exciting future of CNC machining and its potential to shape industries worldwide.
Table of Contents
Understanding CNC Machining
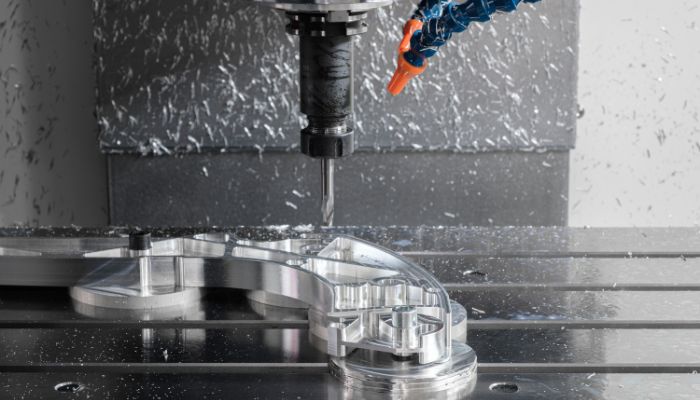
Computer Numerical Control (CNC) machining is a type of manufacturing that uses numerical controls to run cutting machines. This technique allows the exact molding of materials like plastic, metal, and wood into complex components. The benefits of CNC machining include –
- Precision – CNC machines can make products with fine tolerances of ±0.01 mm.
- Consistency – Automated procedures provide consistency during lengthy manufacturing runs.
- Flexibility – CNC machines are perfect for both small-batch and mass manufacturing because they can be programmed to produce a wide range of items.
Key Trends Shaping The Future Of CNC Machining:
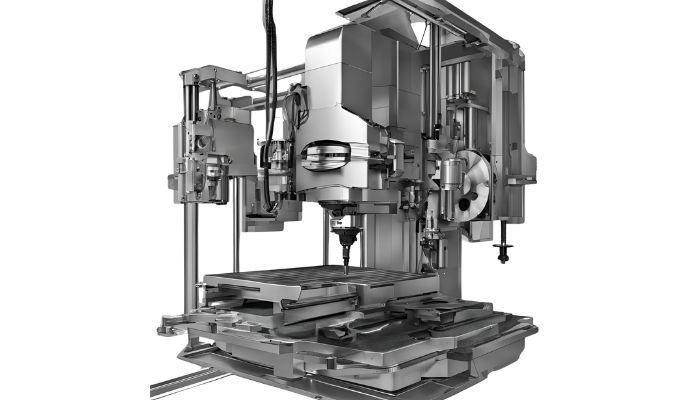
1. Additive Manufacturing and CNC Machining Convergence
The combination of additive manufacturing (3D printing) with CNC machining provides a synergistic approach to component production. Additive manufacturing can create complex geometries that are often difficult to achieve through traditional machining alone, while CNC machining is employed for finishing and precision operations. This hybrid approach allows manufacturers to produce highly customized and intricate components, expanding the design possibilities for various applications.
2. Artificial Intelligence and Machine Learning
Machine learning (ML) and artificial intelligence (AI) are transforming CNC machining by providing possibilities for predictive maintenance, optimizing tool path generation, and improving quality control. AI-powered systems can scan huge amounts of data for patterns and anomalies, which leads to preventive maintenance procedures that increase equipment uptime. CNC component manufacturers may boost production and reduce operational costs by using AI and machine learning.
3. Internet of Things (IoT) and Industry 4.0
IoT-enabled CNC machines can collect and transmit real-time data on their performance, allowing for remote monitoring and control. Analysis of this data can increase overall efficiency, decrease downtime, and enhance manufacturing operations. IoT and other technologies are contributing to Industry 4.0, which is bringing in a new era of intelligent production. As manufacturers embrace these digital advancements, they will gain insights into their operations that were previously unattainable.
4. Advanced Materials and Coatings
CNC machining is becoming more and more popular as new materials like composites, ceramics, and high-strength metals are developed. These materials may be used to make components that are highly resistant to high temperatures, corrosion, and wear. Additionally, advanced coatings can be applied to CNC machined components to enhance their surface properties and extend their lifespan, making them ideal for demanding applications.
5. Automation and Robotics
Automation and robotics play a crucial role in increasing the efficiency and productivity of CNC machining processes. Robotic arms can load and unload parts, perform complex machining operations, and assemble components, streamlining the production workflow. Automated systems can also optimize material handling and logistics, reducing the reliance on manual labor and allowing manufacturers to focus on more value-added tasks.
6. Customization and Small Batch Production
The demand for customized solutions is rising, driven by industries that require unique and specialized components. CNC machining technology allows for quick adjustments in the production process, making it ideal for small batch production and tailored solutions. CNC components manufacturer are leveraging this flexibility to cater to niche markets and meet the specific needs of their clients, positioning themselves as innovative partners in the manufacturing landscape.
7. Enhanced Training and Skill Development
As CNC machining technology advances, the need for skilled operators who can navigate these sophisticated systems is paramount. Manufacturers are spending money on educational programs to provide their employees with the skills required to operate and maintain cutting-edge CNC equipment. This focus on skill development boosts output and guarantees that businesses maintain their competitiveness in a sector that is changing quickly.
What Challenges and Considerations Lie Ahead For The Future Of CNC Machining?
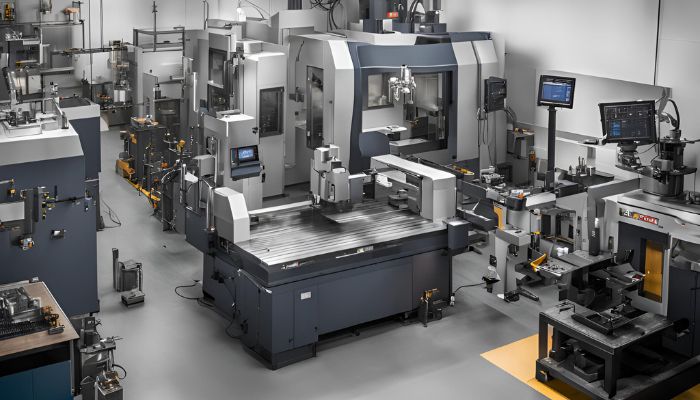
Although CNC machining has a bright future but there are a some of issues and concerns that must be resolved –
- Skill Gap and Workforce Development – There is a lack of competent workers in the sector to run and maintain advanced CNC equipment. To address this, manufacturers should engage in comprehensive training initiatives to upgrade their current staff and bring in fresh talent in order to overcome this. This includes training on the latest CNC technologies, programming software, and machine maintenance.
- Cybersecurity – As CNC machines become increasingly connected, cybersecurity risks need to be mitigated. CNC components manufacturer should safeguard their systems from hacking by using comprehensive cybersecurity measures that include firewalls, intrusion detection systems, and frequent software upgrades.
- Initial Investment and Return on Investment (ROI) – The initial investment in advanced CNC technology can be significant. However, these technologies can offer significant long-term benefits, such as increased productivity, improved product quality, and reduced labor costs. To maximize ROI, manufacturers should carefully evaluate their needs and select the right technology for their specific applications.
- Adapting to Evolving Technologies – The rapid pace of technological advancement in the CNC machining industry requires manufacturers to stay updated on the latest trends and innovations. Working with technology suppliers, going to industry conferences, and receiving additional training may all help to achieve this. By adopting new technologies and changing to new demands from customers, manufacturers can remain competitive in the future.
How The Future Innovations in CNC Machining Will Impact Various Industries
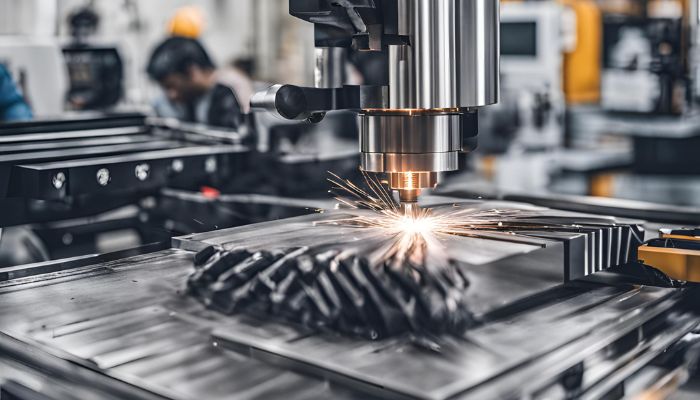
The innovations in CNC machining technology will have profound implications across multiple industries:
- Aerospace – Precision components produced through advanced CNC machining are vital for aircraft manufacturing, where safety and performance are paramount.
- Automotive – As vehicles become more complex with electric and autonomous technologies, the demand for high-precision machined parts will continue to grow.
- Medical Devices – The medical industry relies heavily on custom machined components for devices that require stringent quality standards and precision engineering.
- Electronics – With the rise of smart devices, there is an increasing need for intricate components that can be efficiently produced using modern CNC techniques.
Global Precision Pvt Ltd – Driving The Future Of CNC Machining
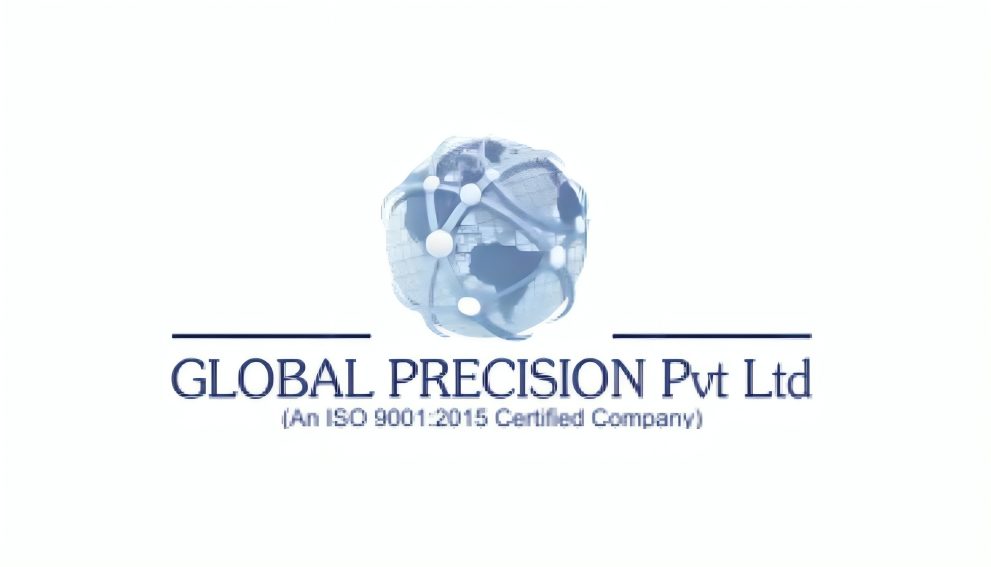
As a leading name among CNC machined components manufacturers, Global Precision Pvt Ltd is dedicated to driving innovation in the CNC machining sector. Our cutting-edge facilities, outfitted with cutting-edge gear are dedicated to producing high-quality CNC turned and CNC milled parts.
Our commitment to precision engineering ensures that every component we manufacture meets international standards, establishing us as a trusted partner across various industries, including automotive, aerospace, and electronics.
At Global Precision, quality is paramount. We adhere to rigorous quality control processes and maintain timely delivery schedules to meet our clients’ needs. Our customized solutions are tailored to specific requirements, allowing us to stay effective in a constantly changing market situation.
Conclusion
The future of CNC machining looks promising, with new developments on the way. By adopting new technology and being dedicated to innovation, Global Precision Pvt Ltd is well-positioned to have a significant impact on how manufacturing develops in the future. Whether you need simple or complex components, our team of experts is dedicated to providing you with the highest quality products and services.