CNC (Computer Numerical Control) machining has transformed the production of copper parts which offers increased enhanced precision, efficiency, and versatility. As industries increasingly rely on copper for its excellent conductivity, thermal properties, and machinability, understanding the intricacies of CNC copper machining becomes crucial.
By automating the process, CNC machining improves speed, accuracy, and precision, making copper parts manufacturing more manageable. In this blog post, we’ll discuss the key things you should know about copper CNC machining.
Table of Contents
Advantages Of Copper CNC Machining:
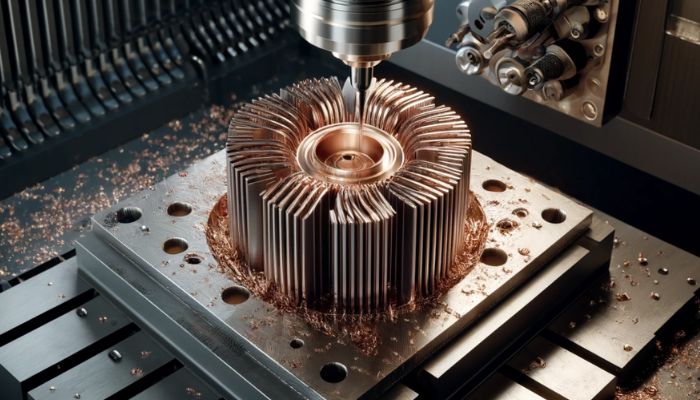
CNC copper machining offers several advantages that make it a preferred choice for manufacturers –
- Precision and Accuracy – CNC machining ensures exceptional accuracy and precision in copper components. The most precise criteria can be met by the computer-controlled cutting tools, which can create parts with precise dimensions and close tolerances.
- Efficiency and Productivity – CNC machines make similar parts with little variation by following preprogrammed instructions. This consistency is vital for mass production and quality assurance.
- Versatility in Design – It may be difficult to create complicated and intricate patterns using traditional methods, but CNC machining’s versatility makes it possible. This versatility is particularly beneficial in industries requiring customized components.
- Material Optimization – Copper is a recyclable metal, making it a sustainable choice for manufacturing. CNC machining processes can be optimized to minimize waste and maximize material utilization, further contributing to environmental sustainability.
- Repeatable Quality – With CNC machining, manufacturers can achieve reliable and repeatable quality across large production runs, which is essential for maintaining product standards.
Key Considerations For Successful CNC Copper Machining:
It is essential to take into account the following elements in order to guarantee good CNC copper machining –
1. Choosing The Right Copper Grade
The properties of copper can vary depending on the alloying elements added. Typical copper alloys consist of –
- Pure Copper (C10200) – It provides excellent machinability, ductility with good electrical and thermal conductivity.
- Brass – A copper and zinc alloy prized for its machinability, strength, and resistance to corrosion.
- Bronze – An alloy of copper and tin, offering wear resistance, high strength, and corrosion resistance.
The particular needs of the application, such as electrical conductivity, mechanical strength, and corrosion resistance, must be taken into consideration while choosing the right grade of copper.
2. Design For Manufacturability
Designing copper parts with manufacturability in mind is essential for efficient and cost-effective machining. Consider factors such as:
- Part Complexity – Avoid overly complex geometries that may be difficult to machine or lead to tool wear.
- Tolerances – Ensure that specified tolerances are achievable within the capabilities of CNC machining.
- Surface Finish – Determine the required surface finish and select appropriate machining parameters.
- Material Removal Rate – Make plans that take into account the quantity of material that needs to be removed.
3. Setting The Appropriate Feed Rate
The feed rate is a crucial parameter in CNC copper machining. It affects factors such as tool life, surface finish, and material removal rate. A higher feed rate can improve productivity but may also lead to increased tool wear. The ideal feed rate is determined by a number of variables, including the desired surface finish, cutting depth, and tool type.
4. Select The Appropriate Tool Material
Choosing the right tool material is pivotal for effective CNC machining of copper. Copper’s softness can lead to high chip formation and tool wear, making it essential to use tools specifically designed for machining copper. Carbide or high-speed steel (HSS) tools with sharp edges are ideal for achieving the desired surface finish and dimensional accuracy. Regular tool sharpening is also recommended to maintain optimal performance.
Applications Of Copper CNC Machining:
- Electronics – Because of its excellent electrical conductivity, copper is an essential part of modern gadgets. CNC machining is used to fabricate intricate parts such as connectors, printed circuit boards, and heat sinks.
- Heat Exchangers – Since copper has such good thermal conductivity, it is frequently employed in heat exchangers. The performance and efficiency of heat exchangers can be improved by producing intricate parts with accurate dimensions thanks to CNC machining.
- Automotive – Copper is utilized in many vehicle components, such as radiators, electrical harnesses, and brake systems. The automotive industry has tight standards, and CNC machining is utilized to make complex copper parts that meet those expectations.
- Machinery and Equipment – Many parts of machinery and equipment, including shafts, gears, and bearings, are made of copper. High-precision copper parts for various applications can be produced through CNC machining.
Conclusion
Copper CNC machining is a crucial process in modern manufacturing, offering precision, efficiency, and high-quality results. By understanding the advantages of CNC machining and adhering to key considerations such as selecting the right copper grade, designing for manufacturability, setting appropriate feed rates, and choosing suitable tool materials, manufacturers can enhance their production processes.
At Global Precision, we have the expertise and state-of-the-art equipment to handle all your copper CNC machining needs. Our skilled engineers and operators ensure that your parts meet the highest industry standards while adhering to tight tolerances and precise specifications.